Standard single-process CNC machine tools may be a thing of the past at PBM Inc. now that the shop has acquired its first advanced multi-tasking machine. The Irwin, Pennsylvania, shop manufactures specialty valves, and Stuart Zarembo, company President and CEO, predicts that, as the shop replaces its mills and lathes, it will most definitely do so with machines that provide multi-tasking functionality.
“There is just too much set up time involved with our single-process machines, so they fall short in terms of cost-effectiveness for our quick run, small lot size parts with extremely tight deliveries,” explained Zarembo. “In most instances, setting up multiple machines takes longer than does actually machining a job. While multi-tasking, on the other hand, dramatically reduces our set up times and allows us to complete parts in one setup and on one machine.”
PBM Inc. Success Story
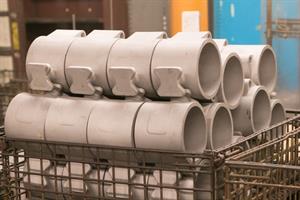
PBM, with 90 employees, develops about 600 new designs per year, and on average, it processes about 1,800 individual work orders annually. According to Zarembo, the shop’s continued success as a leader in specialty valves hinges on instantaneous customer responsiveness and the shortest lead times in the industry – a claim that was recently put to the test with one of the largest orders in PBM’s history. It was this job that also spurred the shop to acquire its first Multi-Tasking machine, an INTEGREX e-420H-S from Mazak.
This order consisted of valves machined from corrosion and abrasive-resistant materials with specific deadlines that had to be met along with penalty clauses if those deliveries were late. In fulfilling all the customer’s requests and meeting the deadlines, PBM worked with a local contract-machining supplier that uses Mazak Multi-Tasking machines.
“We saw the performance of these machines and, as a result, decided to incorporate the technology into our own processes,” said Zarembo. “We evaluated several other brands as well, but to us, Mazak had a much larger installed base and extensively more experience when it came to multi-tasking machines. Plus, both Mazak and its local distributor A.W. Miller impressed us greatly with their responsiveness to our needs.”
PBM’s INTEGREX e-420H-S delivers DONE IN ONE® part processing capability. It features two opposing turning spindles, each with 40-hp output, maximum speeds of 4,000 rpm and C-axis control in 0.0001-degree minimum increments. For multi-tasking operations, a strong 30-hp, 12,000-rpm integral motor milling spindle with CAT 40 interface swivels 240 degrees in the B-axis and allows for 5-axis machining at either turning spindle.
The machine, with a 3” through-spindle bar capacity, can cut part diameters up to 26.38” and accommodates those almost 80” long and weighing approximately 1,000 lbs. PBM also opted for a maximum tool storage capacity of 120 tools on its machine to further boost part processing versatility and support continuous multi-tasking operations.
For PBM, the ample tool storage and DONE IN ONE capability of the INTEGREX e-420H-S generate significant time savings. Zarembo pointed out that, excluding initial part program development, the shop has experienced an average of 75 percent savings on set-up times and 50 percent on cycle times, while also eliminating some work in process (WIP).
The majority of PBM customers are from the pharmaceutical/biotech, consumer/personal care products, chemical, energy and other industries. PBM manufactures primarily ball-type valves that are custom designed and built to fulfill the exact needs of each customer’s individual applications. Most involve uncommon types of liquids, those that are highly corrosive or abrasive, or that are thick in viscosity. And in almost all instances, the valves have specific dimensional requirements.
A perfect example of PBM’s specialty valve capabilities is what it refers to as Fabflex® headers. Again, built to a customer’s specific requirements, a Fabflex® header is a pipe (header) with several valves on it to form a modular system that is then easily installed.
In one particular application involving product mixing in continuous batches, PBM designed and built a Fabflex® header modular system that featured an 8”-diameter, 11’-long header made out of stainless steel with flanged ends and 23 automated valves. The product’s various ingredients feed in through the individual valves and mix together. And it should be noted that PBM is the only valve supplier that will produce such a fully automated system.
Most of PBM’s valves range in size from 1/2” to 12” from castings or bar stock. Materials include carbon and stainless steel, bronze, aluminum and special alloys such as duplex stainless, Hastaloy and titanium.
Valve processing requires about 60 percent turning operations and 40 percent milling. There is both I.D. and O.D. turning and boring work along with hole drilling and the occasional complex contours. With the first turning spindle on the INTEGREX e-420H-S, the shop machines the front side of a part. The machine then hands it off to the second spindle for backworking. After which, the part comes off the machine complete and processed in one setup.
“For most of our setups on the INTEGREX e-420H-S, we simply clamp parts in a turning chuck,” commented Matt Walters, CNC machinist at PBM Inc. “Plus, the machine’s conversational programming makes that aspect of setup fast and easy as well. Without the Mazak, we’d have three or four different setups over a lathe and a mill with lots of parts staged by each machine. And with the Mazak, we can load 4’ lengths of bar stock and cut multiple parts to eliminate the time it takes to saw a lot of individual part slugs.”
Because the INTEGREX e-420H-S was the shop’s first multi-tasking machine, training from Mazak was important to PBM. Five of the shop’s CNC machinists went through Mazak training and later advanced training. Currently, two machinists run the machine, each assigned to one of the two 10-hour shifts the machine operates between Monday through Thursday and sometimes on Fridays and Saturdays. However, Zarembo added that those hours of operation continue to increase as the shop gets fully up to speed with the machine.
Zarembo, who has been leading PBM since 1991, spearheaded the first major investment in the shop’s machine tools back in the mid-1990s. That investment added three CNC lathes, two CNC mills and a Swiss-style turning machine.
“While we could have purchased more CNC mills and lathes, we went with the Mazak,” said Zarembo. “And now going forward, we will most likely opt for nothing but advanced multi-tasking machines like our INTEGREX e-420H-S.”