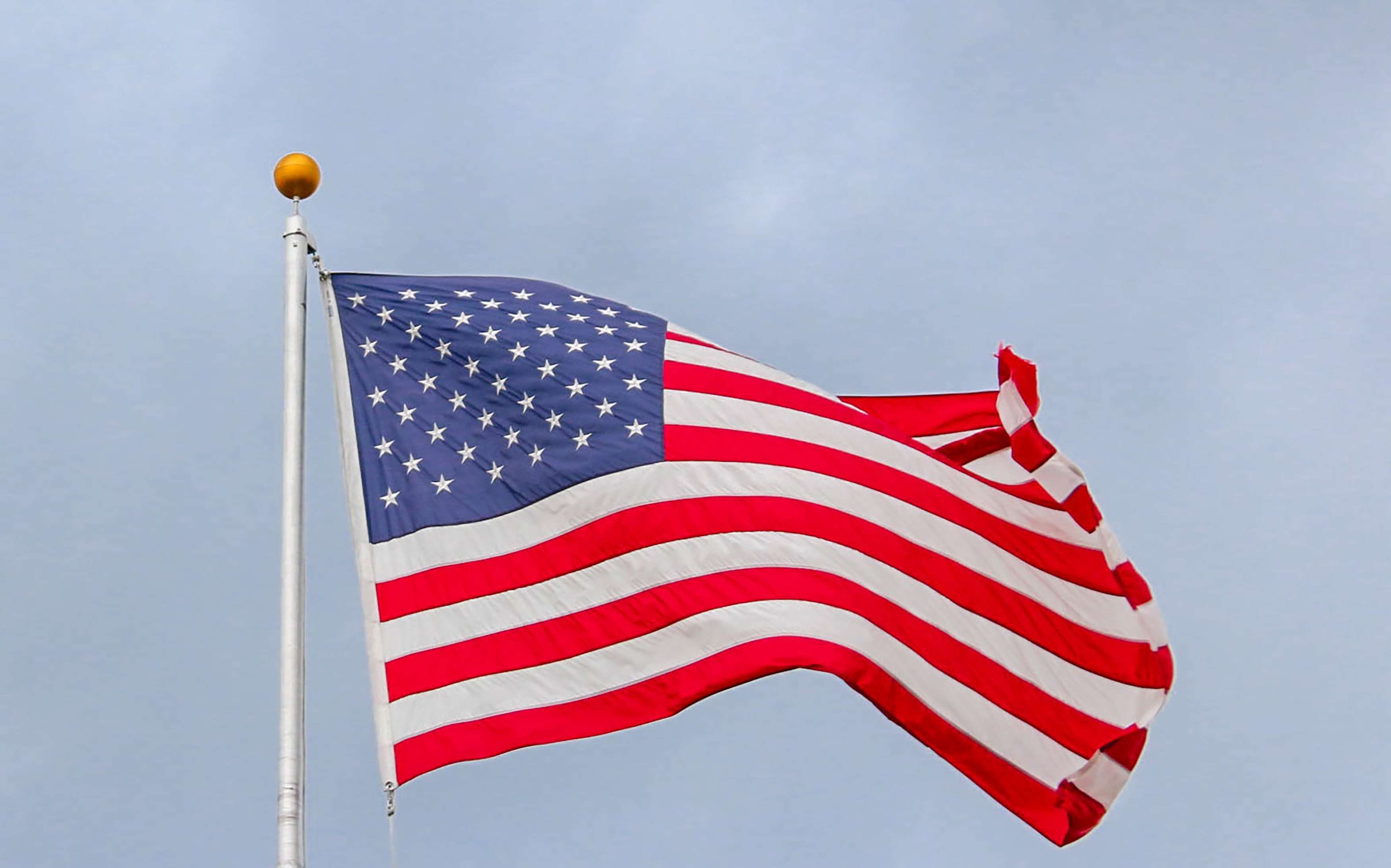
The COVID-19 pandemic has revealed many heroes among our neighbors, from the doctors and nurses fighting on the front lines to the grocery store and sanitation workers keeping the world running. Manufacturing, both in the medical industry and beyond, has its role to play as well, and heroes throughout the industry have been doing their part. But as the Reshoring Initiative’s Harry Moser pointed out in a recent episode of Mazak’s All Axes podcast, the crisis is also revealing the limitations of a global supply chain – and pointing toward how to fix it with advanced domestic manufacturing.
In normal times, the fragility of the supply chain isn’t an issue for many Americans. It may be true that 97% of antibiotics are imported, for example, but as long as shelves stay stocked, the distance the pills traveled to the pharmacy isn’t important for most customers. But this system only works when supply and demand remain stable; during periods of abnormally high demand, the global supply chain can’t keep up. And when the U.S. is producing only 1.66 million surgical masks per day to China’s 115 million, that’s an issue, especially when the Department of Health and Human Services estimates that pandemic conditions may require as many as 3.5 billion masks in the U.S. alone.
Increasing domestic production capacity isn’t just a matter of national security, however. In fact, many shops are using the present crisis to reconsider how much of a negative impact offshoring has on their profitability. Few manufacturers study the topic closely – about 60% of companies only look at the sticker price for production. And by doing so, they miss roughly 20% of the total cost of offshoring, from travel costs to the risks to intellectual property.
This “total cost” model, which the Reshoring Initiative explores in its Total Cost of Ownership Estimator® calculator on its website, considers 30 different cost and risk factors to help manufacturers establish the actual cost of sourcing materials and products abroad. What many shops discover is that, after accounting for every factor that goes into the actual costs of production, domestic production is actually cheaper.
As more companies discover this, and as more jobs return home, young people will start to gravitate to the industry once again. Now that it looks like a stable career path with a future in the U.S., high schoolers see apprenticeships as a great way to jump start their working lives. And as companies realize the profit potential in reshoring, they will invest in productivity-enhancing equipment like automation and Multi-Tasking technology that will allow their businesses to grow even further - a topic that will be discussed in an upcoming Mazak All Axes podcast and blog.
This kind of virtuous cycle will be vital for rebuilding manufacturing here in the U.S. – and preparing the country for the next crisis it may face. To learn more about the benefits of reshoring, visit ReshoreNow.org and listen to Harry Moser’s interview on the All Axes podcast.